Our filters solutions!
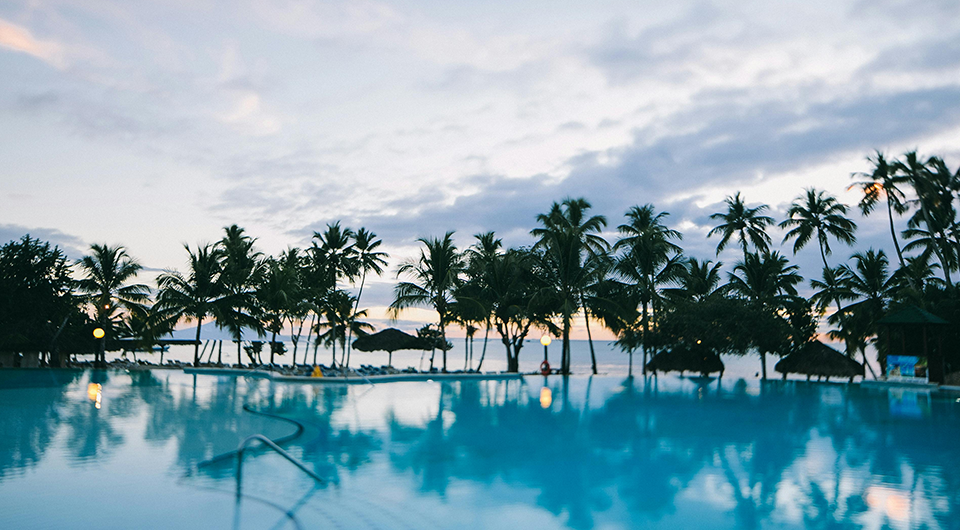
Hayward® is at the forefront of technology in water-treatment technology with more than 35 years experience in the manufacture and development of solutions implemented in fiberglass-reinforced polyester (FRP) filters.
Our products are aimed at professionals for solutions at different pressures, for a variety of applications such as water treatment, swimming pool filtration, aquatics parks, spas and aquariums…
All Hayward® Commercial Aquatics filters:
- Are manufactured in accordance with standard ISO 9001:2025.
- Are subject to strict pressure and leak detection tests systems in accordance with the standard: UNE-EN 13121-3.
Our bobbin-wound filters (Fiberglass-Reinforced Polyester)
Our bobbin-wound filters manufacturing process
Elastic body resistant to high pressure with less weight
Their manufacturing method is based on a combination of techniques (lamination, coiled and wound) and materials (fiberglass fabrics and resins) whose final result is a tank with an elastic body providing high resistance to the operating pressures with minimal wall tickness. This technique markedly reduces the weight of the filter, and it can operate with significant diameters and heights.
In addition, as a distinguishing feature of our manufacturing process, the filters are not painted. When performing the winding process, the polyester fiberglass thread is dyed. Then, it is cured in an oven, giving the tank's surface a finish that prevents sweating effects once installed, together with the careful treatment of the resins from its manufacture.
High chemical resistance
The chemical resistance of the filters comes from the chemical resistance of the polyester in their different viarieties of very low emissions resins, using, in each case, the most suitable for the application.
PVC interior liner
In certain circumstances, it is combined with a PVC component in the interior of the tank, such as in the case of installations where ozone generators are used for disinfection. In addition, this finish is recommended for applications that work with seawater, given that it will not be affected in any way, by the high corrosion capacity from this environment and its sediments.
Wide range available
The filters supplied are designed for a permissible maximum pressure of: 2.5, 4 and 6 bar. The usual operating pressure value must always be maintained, at least, 20% below the permissible maximum pressure value.
Options
The filters can be supplied with options that enable them to be adapted to the specific needs of each application, from the triple-effect relief valve installed on the cover, to an oval or circular side port, as well as sigh glasses etc.
All the filters are manufactured according to the relevant European standards: the hydraulic tests are carried out at 1.5 times the maximum operating pressure, the inlet and outlet connections are DIN flanges, and all indications related to the calculations that measure filtration expansion zones, speeds and flows have been followed. Each filter comes with an instruction manual.
Our collector types
There are two types of collectors: with a grill arms system, and with a nozzle plates systems.
Bobbin-wound filter with arm collectors
The arm collector system is versatile, economical and easy to maintain. It is recommended in installations where there is a need for filtration using sand, glass or other material with a granulometry greater than 0.35 mm, in accordance with the arm collectors movement. The cleaning-rinsing of filters with arm collectors should be performed with water; air-blower systems or similar must never be used, as these would damange the arm collectors. The pressure during the washing operation should never be greater than 1 bar for filters with arm collectors.
Arm collector filters come with lifting eyes, 1" manual air-release ball valve, sand discharge, 1" drain, pressure guide manometer next to the indicator of the maximum operating pressure that the filter has been subjected to.
The number of arms and their length is determined by the flow to be filtered and the diameter of the filter.
The arm collectors water flow is limited to 0.35 mm.
Our bobbin-wound filters nozzle plates
The nozzle plates system provides better water distribution during the filtration process. This filter technology also allows the use of a blower for backwashing and washing the filter mass. This reduces water consumption during the filter washing sequence by almost 60%.
In fact, the filter media is unpiled by air coming from the glowers and then washed with the air/ water mixture. For this type of installation, we recommend automatic management of the filter valve battery. For this we offer pneumatic or electric valves with the control box which will trigger the washing sequences according to the load loss or a perioditicty predetermined by the user.
Our technicians remain at your disposal for the dimensioning of this filter, the blowers and the control of the automatic valves.
By default, the nozzle water flow is limited to 0.2 mm, offering better filtration quality.
The nozzle plates feature an access cover for inspecting the bottom of the filter, so that cleaning and maintenance tasks can be performed.
Cleaning our bobbin-wound filters
Cleaning the filter bed
The filter bed creates thousands of flow channels that collect the solid residues and impurities contained in the filtered water. Over time, these sediments block the flow of water, and the filter needs to be cleaned so it remains in optimum working conditions, flushing the dirt left on the filter bed down the drain.
To clean the bobbin-wound filters, we recommend following the instructions detailed in standards DIN 19605 and DIN 19643. We recommend following this process for the duration of 7 minutes as a speed of 50 m³/h/m². To prevent the loss of filter bed in the drain, it is not recommended to exceed the mentioned speed. The pressure during the washing operation should never be greater than 0.8 bar for filters with nozzle plates.
Cleaning using air and water
This cleaning option is recommended only for filters with nozzle plates. If this operation is required, we recommend using one or several blowers, generating a total aeration speed of 50 m³/h/m² within the filter operating at pressure range between 250 and 300 mbar, taking into account that the jointly exerted pressure by both the air and the water never exceeds 0.8 bar at any time.
The blowers will have a syphon at the top of the filter with an anti-return valve to prevent water from entering. Additional load loss generated by the different accessories installed must be taken into consideration.
We recommend installing an additional safety valve on the blower to prevent excess pressure, which may damage both the filter and the blowers. The use of a progressive-start device on the blower is recommended to prevent sudden variations in air pressure entering the filter (frequency converter, soft starter, etc.). We recommend that the air enters the filter from the valve manifold. Never use an air compressor to carry out this operation, as this would seriously damage the filter.
You will like also ...
ALL NEWS